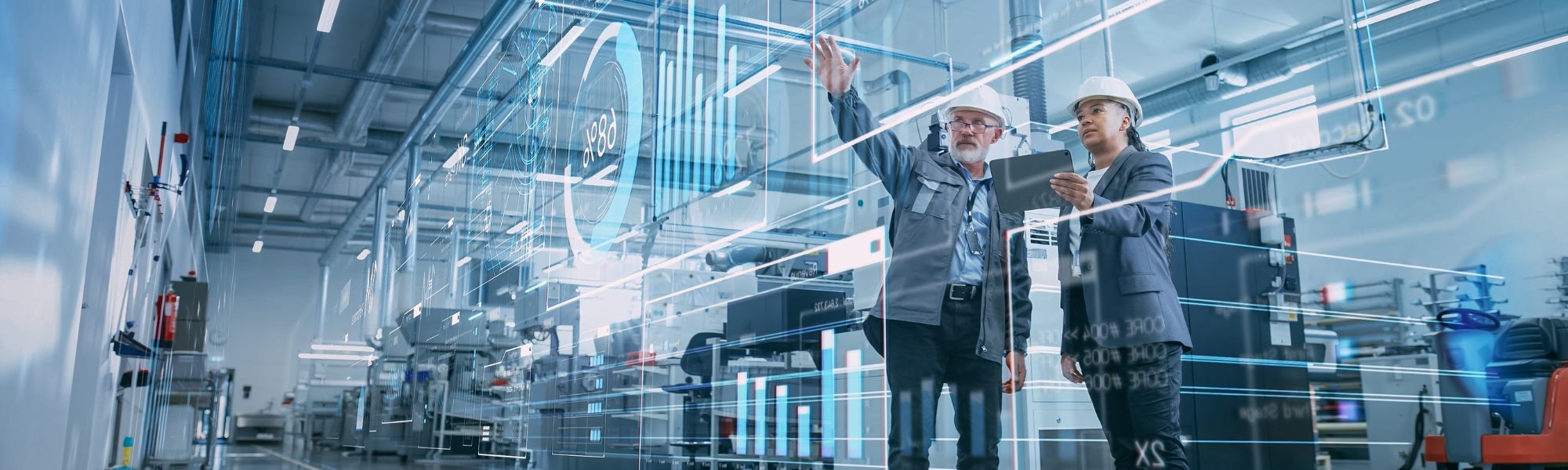
Instrumentation is arguably a discipline where the diversity of physical phenomena is used to deliver optimal engineering solutions. Many sensors are electrical by design: strain gauges, piezo-electric accelerometers, piezo-resistive sensors, etc. Optical sensors operate on a different principle, and many of them rely on fiber Bragg grating.
The principles of fiber Bragg grating (FBG) technology are as follows. At manufacturing, short sections of an optical fiber are exposed to an intense UV light whose wavelength is accurately controlled. These short sections are called fiber Bragg gratings. Inside the fiber, the exposure generates many reflection points that create a reflection of a particular wavelength of incident light. The distance between the reflection points of one specific fiber Bragg grating is always equal. The wavelength that matches exactly the distance between two reflection points is reflected by the grating. All other wavelengths are transmitted through the grating without being reflected or damped. By knowing the spectrum of the incident light – between 1,500 to 1,600 nanometers for QuantumX MXFS – and measuring the wavelength of the reflected light, an optical interrogator can measure the space between reflection points at the grating.
When the fiber is connected to a mechanical structure, the strain of the structure bends the fiber and changes the distance between reflection points. The wavelength of the reflected light changes. The optical interrogator measures that change and the strain can be calculated.
Fiber Bragg gratings are therefore sensitive to strain. But they are also sensitive to temperature. This means that a strain measurement of a sensor that is subjected both to strain and temperature is also influenced by the temperature change. But this effect is well characterized and easy to compensate, with several methods available.
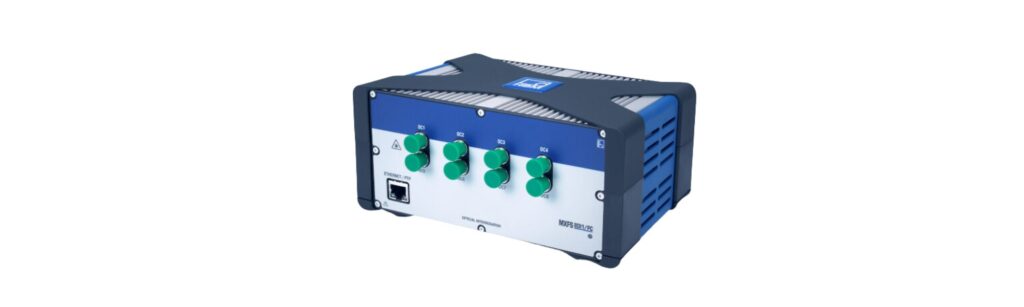
The resulting optical sensors, using variation of light wavelengths instead of variation of electrical quantities, offer several advantages over traditional sensors: immunity to electromagnetic interference, high fatigue limits, multiplexing capabilities, negligeable losses, etc. But this does not mean that traditional electrical sensors do not offer advantages: lower costs if only a few sensors are needed, availability of previously purchased data acquisition systems, existing in-house skillsets, etc. For monitoring large new structures, combining traditional and optical sensors is often the ideal solution.
NVMS and HBM offer a fantastic choice of sensors and data acquisition systems (DAQ) covering and integrating both technologies. HBM optical sensors can measure strain, temperature, tilt, displacement, force, and acceleration. See newLight | Optical Fiber Sensor | Fiber Optic | FBG (hbm.com)
QuantumX DAQ portfolio includes modules for both “traditional” sensors and optical sensors. QuantumX MXFS is the optical interrogator. All signals can be integrated in catman, offering the ideal measurement chain.
For more information, please contact info@nvms.com.au
Author: Christian Ebel (MEng, MBA, MIEAust) – Business Manager, Test & Measurement
The Latest
How can we help you?
Our team of experts are ready to help answer your questions and provide solutions for your unique situation. Get in touch today.